Weekly kaizen
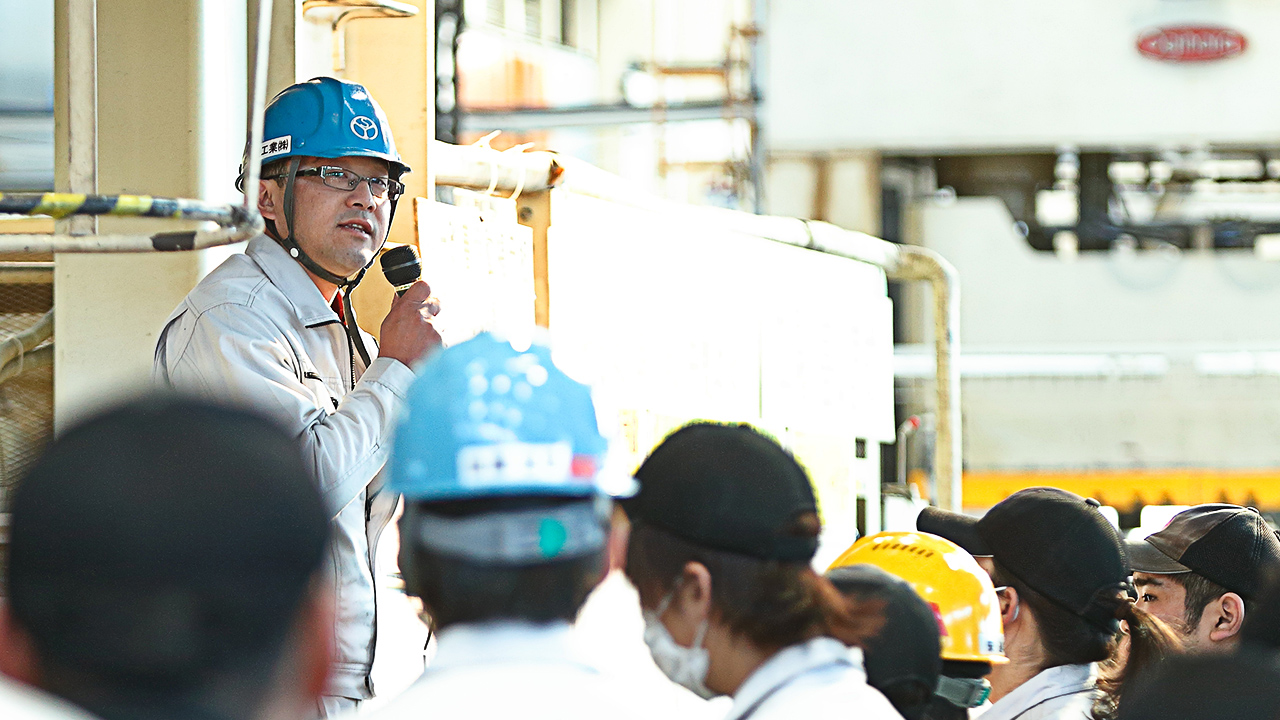
Five teams for Kaizen activity in company are grouped , and each team makes presentation on the improvement result every week.
Since May 2005, Yamaguchi-Seiki has been having weekly Kaizen activity . Thist is the ‘Kaizen in workplace’ according to the Toyota production system. We have 6 teams of “Engineering Sales Dept. , Program Management Dept. and General Management Dept.” , ” CAD Section.”,”CAM Section”,”First Production Dept.” ,”Second Production Dept.” and ” team of General managers” , and each team reports Kaizen result to all emproyees every week.
The weekly Kaizen activity is not the type of QC conference, but it is the purpose to keep ordinary improvement constantly in full participation. For instance, reducing the loss of movement and transportation by work carriage made in house, Increaseing productivity and efficiency by just relocating machinery are examples to improve operations as well as to reduce waste.
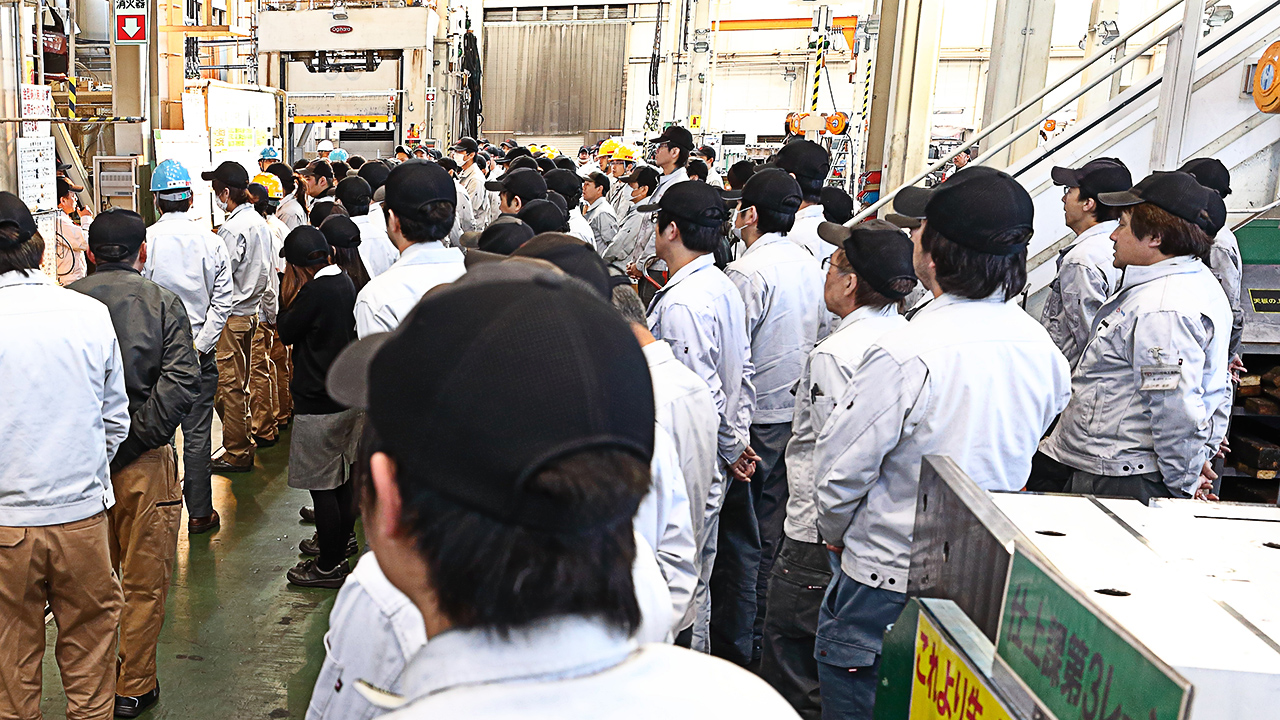
The energy to change the workplace environment greatly, is always to keep cosciousness on the issue to improve.
Employees of Yamaguchi-Seiki are very conscious on the issue ,and have been suggesting Kaizen idea for solutions.
The kaizen results amounted more than 2000 items through 330 times of the weekly presentation by six teams, such as improvement of operation methods, improvement on tools , jigs and equipment in workplace, and improvement on design method and on preparing data and papers to report, all of which are the driving power to convert into positive workplace environment greatly.
The best one amang the improvements will be awarded for excellence and win the trophy , which is one of the gears to raise motivation for all employees.