Second Production Dept. (Finishing Section)
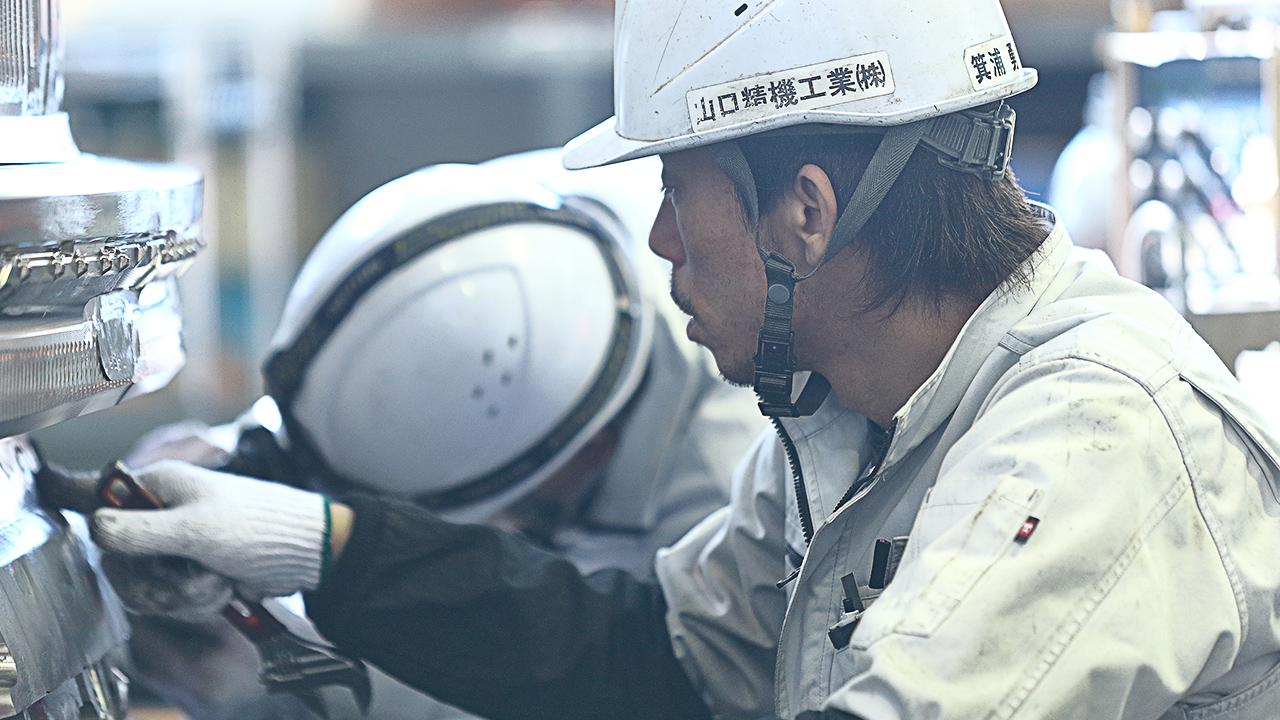
Second Production Dept. (Finishing Section)
Mold parts machined are precisely finished and assembled at Second Production Dept. and ready for delivery to customers.
This Dept. assemble all the parts finished by the first Production Dept. before shipping to customer. The solid design of mold is created by Engineering Dept. which incorporate ideal elements and the newest technology, and then based on the design, the First Production Dept. manufacture component parts, transfer all the parts to the Second Production Dept. for assembly. After assembly, check finally the quality and accuracy, all of which hone and polish the mold to perfection in dept.-by-dept. process. Yamaguchi-Seiki uphold the slogan as “the concept of ‘back to basics’ is underlying in manufacturing.” and have been “sticking to satisfay needs of customers through our solid mold production”. It is the Second Production Dept. that symbolized the slogan and attitude of the company , who is finally responsible for completing the mold. Before end, plastic parts are prototyped by using the finished mold and our own Injection molding machine in-house, then measured the dimensions to feed back the variations for repairing and building the higher-precisione mold.
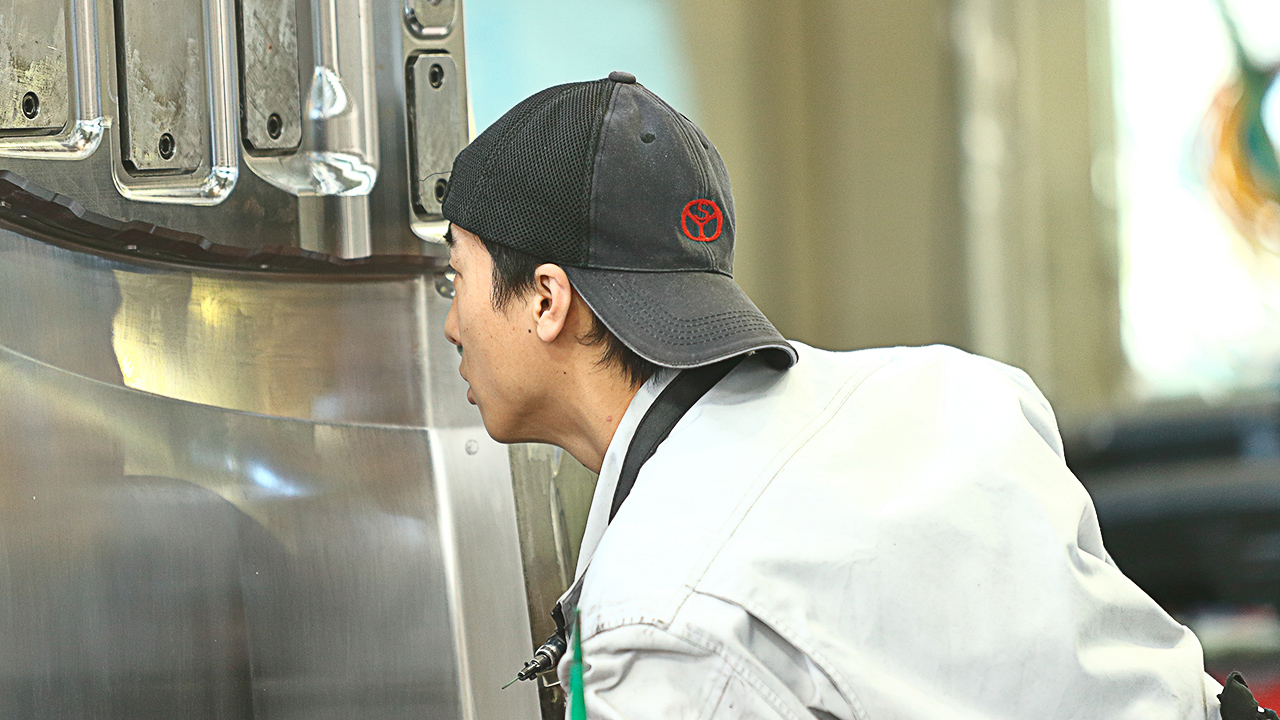
Finishing Section
A realm of artisanship – where we continue to take up the challenges of pursuing ever higher quality in the 1/1,000-millimeter region.
In our prototyping and our operations to correct errors in detailed areas, we sometimes tackle the punishing challenges of working at a thousandth of a millimeter, makes for product-making processes that crystallize the total strengths of people, skills, and equipment to perform grinding at the micron level. The attention that leverages every area of expertise in this way to improve each and every mold with precision and care is connected to our commitment to the basics and fidelity, and bears fruit in the form of the high-quality, high-precision molds we make.
The finishing work for molds is done by hand, and lies within a realm of artisanship that hinges upon intuition and many years of experience. Notwithstanding this, it is also important to transform these skills into data and put them to good use not in the form of individual ability, but as an organization. How to pass down these skills and transmit the skills of artisanship to later generations – we intend to continue devoting effort to creating an organization to take up the next generation of molds.