First Production Dept. (NC machining Section /EDM・Wire-EDM Section)
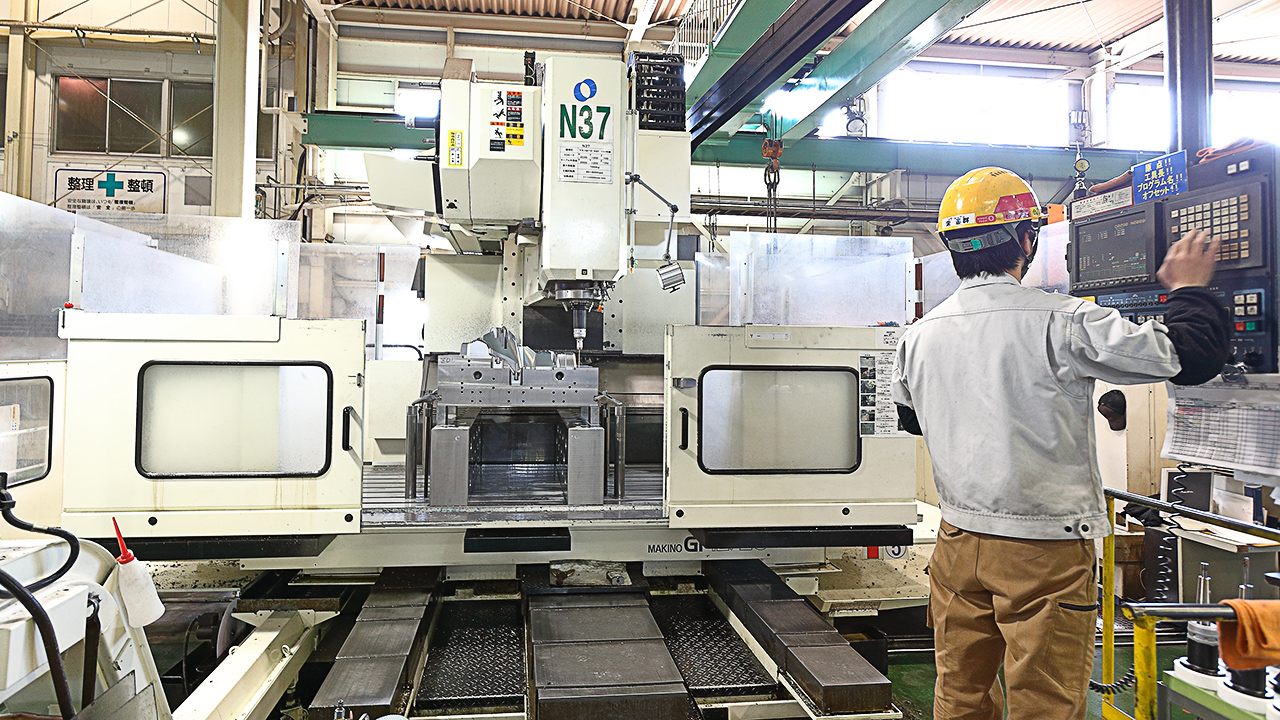
First Production Dept. (NC machining Section /EDM・Wire-EDM Section)
This Dept. manufacture the component parts for mold assembly ,based on the data designed by Engineering Dept.
Bamper mold is one of our main products and the component parts are machined, drilled, and milling-machined by using suitable machine tools. We are proud of the dept., responsible for the major core of mold production. For the more sophysticated production of molds, our dept. gather the requirements from customers and other information, and improve the quality and accuracy of mold by putting the best of our efforts and adding the latest inventive design. The First Production Dept. is constructed by five sections per component such as A section for large and ultralarge mold, B section for middle size mold, C section for component parts , D section for underbody and structure, and E section for electric discharge processing. Metal cutting machine tools including NC high speed Gr processing machine, NC wire cutting machine, NC electric discharge machine, NC milling machine, are effectively used by professional staffs per process, then mold parts with high accuracy are created to satisfy the requirements and desire of customers.
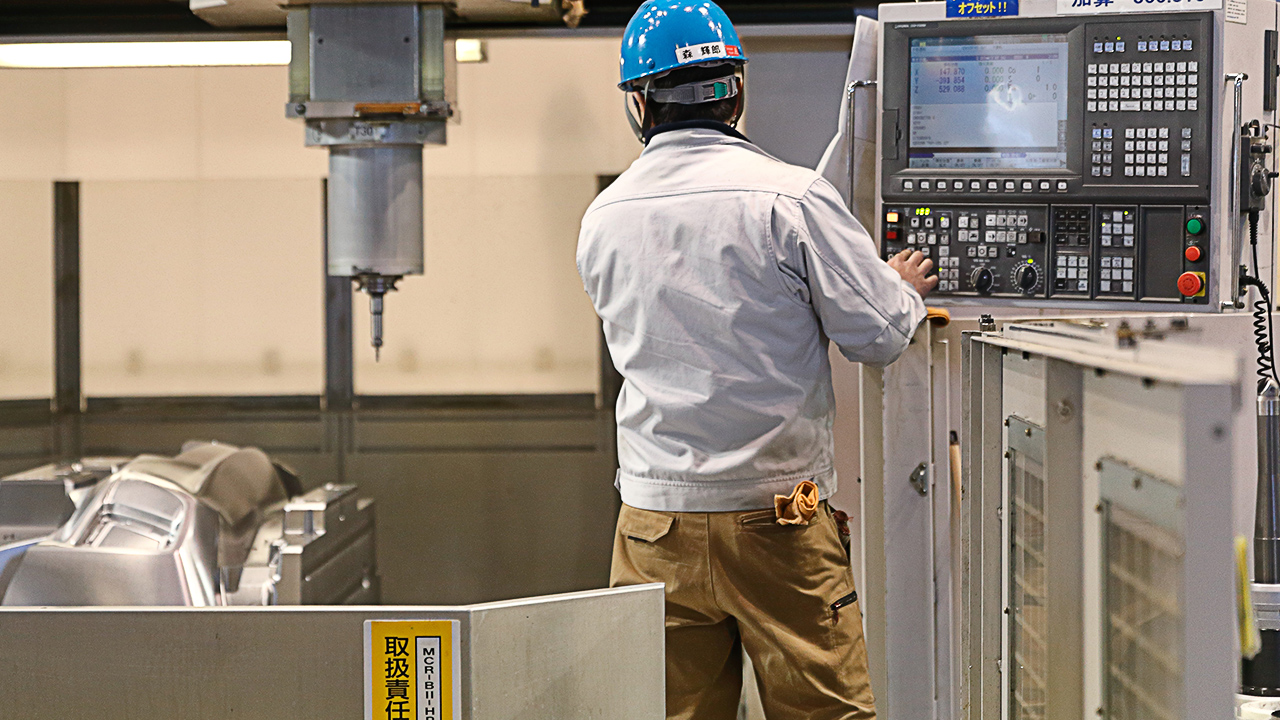
NC machining Section /EDM・Wire-EDM Section
Our sophisticated engineering was appreciated by one of the world-famous atutomotive company.
Since 2002, Yamaguchi-Seiki has started the business directly with the company to manufacture and deliver bumper molds. At the beginning of the business, we were far behind the existing competitors, then we were encouraged and given much spurs by customers and have been learning through trial and error. At 2008 , Yamaguchi-seiki has gradually satisfied the customer and established a very high reputation now, which are source of our pride as the member of the manufacturing dept.